Jak wybrać wózek widłowy do magazynu wysokiego składowania?
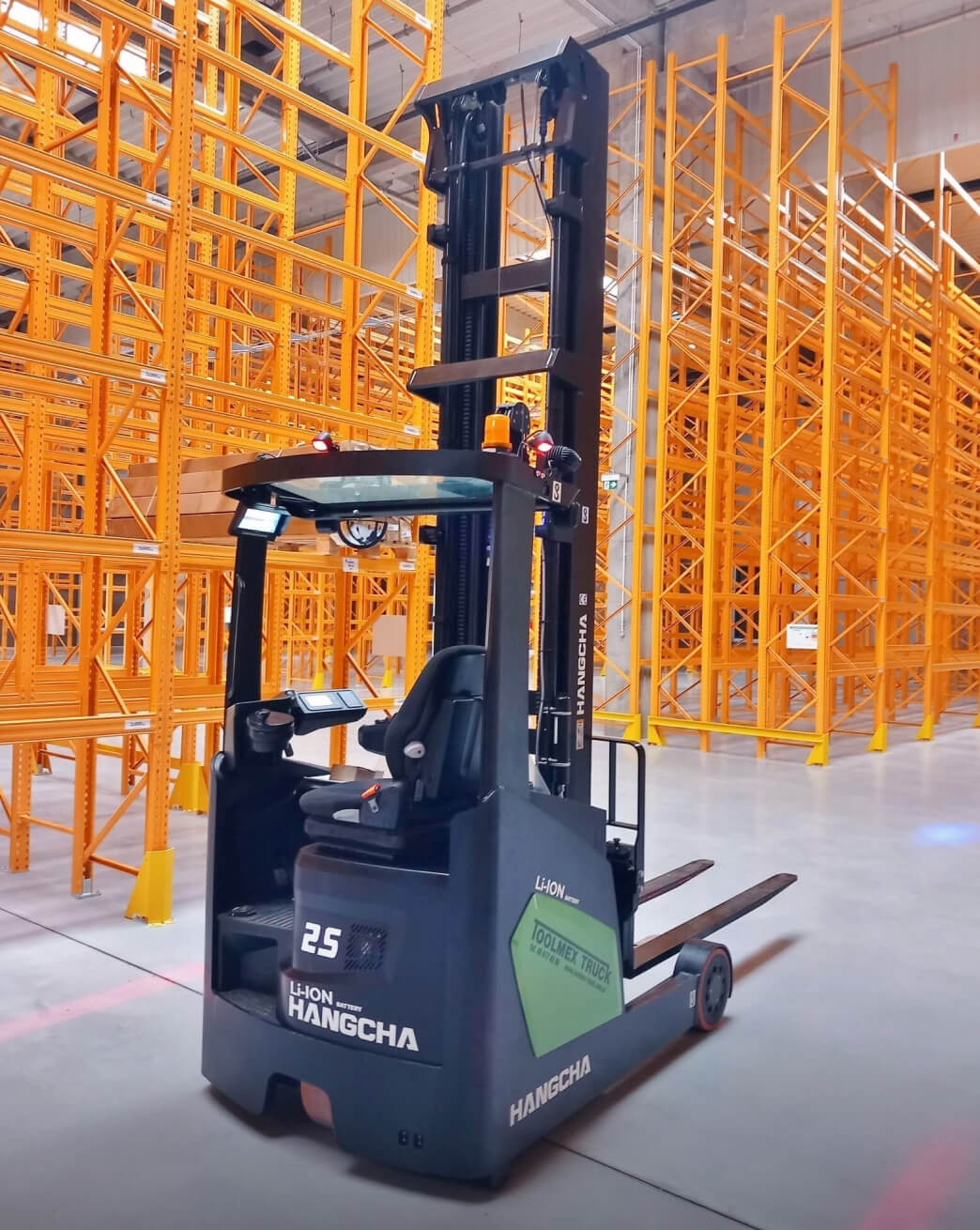
Wybór odpowiedniego wózka widłowego do magazynu wysokiego składowania może być wyzwaniem, zwłaszcza gdy zależy nam na maksymalizacji efektywności i bezpieczeństwa operacji magazynowych. Sprawdź co warto wziąć pod uwagę przy wyborze wózka widłowego, aby ułatwić proces decyzyjny i zapewnić optymalne rozwiązanie dla Twojego magazynu.
Rozpoznanie potrzeb magazynu
Pierwszym krokiem w procesie wyboru wózka widłowego do magazynu wysokiego składowania jest dokładne rozpoznanie specyficznych potrzeb Twojego magazynu. Każdy magazyn jest inny, dlatego bardzo ważne jest zrozumienie jego unikalnych wymagań i warunków operacyjnych. Poniżej przedstawiamy kilka istotnych kwestii, które warto wziąć pod uwagę podczas tego etapu.
1. Wymiary alejek magazynowych
Jednym z najważniejszych czynników, który wpływa na wybór odpowiedniego wózka widłowego, są wymiary alejek magazynowych. Wąskie alejki wymagają wózków o większej zwrotności i mniejszych gabarytach, takich jak wózki wysokiego podnoszenia (reach truck) czy wózki boczne (side loader). Jeśli alejki są szerokie, można rozważyć bardziej uniwersalne wózki czołowe (counterbalance forklift).
- Wąskie alejki (2-3 metry) – wózki wysokiego podnoszenia, wózki boczne.
- Średniej szerokości alejki (3-4 metry) – wózki czołowe, wózki wysokiego podnoszenia.
- Szerokie alejki (powyżej 4 metrów) – wózki czołowe, wózki teleskopowe.
2. Wysokość regałów
Kolejnym kluczowym aspektem jest wysokość regałów w magazynie. Wózki widłowe muszą być w stanie bezpiecznie i efektywnie podnosić ładunki na najwyższe poziomy regałów. Wysokość podnoszenia wózka powinna być dostosowana do maksymalnej wysokości regałów, z uwzględnieniem dodatkowej przestrzeni na manewrowanie ładunkiem.
- Niskie regały (do 5 metrów) – wózki czołowe.
- Średnie regały (5-10 metrów) – wózki wysokiego podnoszenia.
- Wysokie regały (powyżej 10 metrów) – wózki wysokiego podnoszenia, wózki teleskopowe.
3. Rodzaje i wymiary ładunków
Rodzaje i wymiary ładunków, które będą przemieszczane w magazynie, również mają duże znaczenie. Wózki widłowe muszą być przystosowane do obsługi różnych typów ładunków, od standardowych palet po niestandardowe, długie przedmioty.
- Standardowe palety – wózki czołowe, wózki wysokiego podnoszenia.
- Długie ładunki – wózki boczne.
- Ciężkie i nietypowe ładunki – wózki teleskopowe.
4. Potrzeby w zakresie manewrowania i szybkości operacji
Efektywność operacji magazynowych zależy również od zdolności manewrowania wózka widłowego oraz jego szybkości. W zależności od tego, jak intensywne są operacje magazynowe, różne modele wózków mogą lepiej odpowiadać Twoim potrzebom.
- Wysoka intensywność operacji – wózki wysokiego podnoszenia, które są szybkie i zwrotne.
- Średnia intensywność operacji – wózki czołowe, które oferują dobrą równowagę między szybkością a wszechstronnością.
- Niska intensywność operacji – wózki teleskopowe, które oferują dużą elastyczność i zdolność do obsługi ciężkich ładunków.
5. Warunki pracy w magazynie
Warunki panujące w magazynie, takie jak temperatura, wilgotność czy rodzaj podłoża, mogą wpływać na wybór wózka widłowego. W przypadku magazynów chłodniczych czy mokrych, warto wybrać wózki elektryczne lub specjalnie przystosowane do pracy w trudnych warunkach.
- Magazyny chłodnicze – wózki elektryczne przystosowane do niskich temperatur.
- Magazyny mokre – wózki odporne na wilgoć, z antykorozyjnymi powłokami.
- Magazyny z nierównym podłożem – wózki z dużymi kołami i dobrą amortyzacją.
Rodzaje wózków widłowych do magazynów wysokiego składowania
1. Wózki widłowe wysokiego podnoszenia (reach truck)
Wózki te są idealne do pracy w wąskich alejkach i mogą podnosić ładunki na znaczne wysokości, często przekraczające 10 metrów. Ich zaawansowane systemy stabilizacji zapewniają bezpieczne podnoszenie i przenoszenie ładunków.
2. Wózki widłowe boczne (side loader)
Wózki boczne są przystosowane do transportu długich ładunków, takich jak rury czy belki, dzięki możliwości bocznego podnoszenia i przemieszczania towarów. Idealnie sprawdzają się w wąskich przestrzeniach, zapewniając bezpieczne przenoszenie nietypowych ładunków.
3. Wózki widłowe czołowe (counterbalance forklift)
Wózki czołowe są uniwersalne i stabilne dzięki przeciwwadze, co pozwala na efektywne podnoszenie ciężkich ładunków. Nadają się zarówno do pracy wewnątrz magazynu, jak i na zewnątrz, co czyni je wszechstronnym narzędziem.
4. Wózki widłowe teleskopowe (telescopic handler)
Wózki teleskopowe oferują duży zasięg podnoszenia i elastyczność, pozwalając na precyzyjne umieszczanie ładunków na wysokich regałach i w trudno dostępnych miejscach. Są również wykorzystywane w bardziej zróżnicowanych środowiskach pracy, takich jak place budowy i rolnictwo.
Kluczowe parametry techniczne
Przy wyborze wózka widłowego do magazynu wysokiego składowania należy zwrócić uwagę na kilka kluczowych parametrów technicznych:
- Udźwig – udźwig wózka widłowego określa maksymalną wagę ładunku, jaką może podnieść i przenieść. Wybierając wózek, upewnij się, że jego udźwig jest odpowiedni do najcięższych ładunków w Twoim magazynie.
- Wysokość podnoszenia – wysokość podnoszenia to maksymalna wysokość, na jaką wózek może unieść ładunek. Upewnij się, że wózek może osiągnąć najwyższy poziom Twoich regałów, z uwzględnieniem przestrzeni na manewrowanie ładunkiem.
- Wymiary wózka – wymiary wózka, takie jak szerokość i długość, wpływają na jego zdolność do manewrowania w magazynie. Sprawdź, czy wózek będzie w stanie swobodnie poruszać się w alejkach magazynu, zwłaszcza jeśli są one wąskie.
- Zasilanie – wózki widłowe mogą być zasilane elektrycznie, gazem lub dieslem, a wybór zależy od specyfiki pracy w magazynie. Wózki elektryczne są ciche i nie emitują spalin, co czyni je idealnymi do pracy wewnątrz pomieszczeń, natomiast wózki spalinowe są bardziej odpowiednie do ciężkich zadań na zewnątrz.
- Systemy bezpieczeństwa – nowoczesne wózki widłowe są wyposażone w zaawansowane systemy bezpieczeństwa, takie jak systemy stabilizacji, kamery i czujniki. Te funkcje zwiększają bezpieczeństwo operacji, minimalizując ryzyko wypadków i uszkodzeń ładunków.
Bezpieczeństwo i ergonomia
Bezpieczeństwo operacji magazynowych jest priorytetem. Zwróć uwagę na:
- Systemy bezpieczeństwa – wózki widłowe powinny mieć zaawansowane systemy stabilizacji oraz kamery i czujniki wykrywające przeszkody, co minimalizuje ryzyko wypadków. Te funkcje zwiększają widoczność operatora i bezpieczeństwo operacji.
- Ergonomia – ergonomiczne kabiny z regulowanymi siedzeniami i intuicyjnymi elementami sterującymi zmniejszają zmęczenie operatora. Lepszy komfort pracy zwiększa efektywność i wydajność.
- Dostosowanie do specyficznych warunków pracy – wózki powinny być dostosowane do specyficznych warunków pracy, takich jak ochrona przed wibracjami czy pyłem. To zapewnia bezpieczeństwo i trwałość sprzętu.
Koszty eksploatacji i serwisowanie
Przy wyborze wózka widłowego ważne jest również uwzględnienie kosztów eksploatacji i serwisowania. Oto kilka kwestii do rozważenia:
- Koszt zakupu, wynajmu i leasingu – porównaj koszty różnych modeli oraz opcje finansowania. Zastanawiasz się na zakupem, wynajmem bądź leasingiem? Sprawdź nasz wcześniejszy ARTYKUŁ, aby dowiedzieć się więcej na ten temat.
- Koszty paliwa/energii – sprawdź, jakie będą koszty zasilania wózka w dłuższej perspektywie.
- Dostępność części zamiennych i serwisu – upewnij się, że wózek będzie łatwy w utrzymaniu i że dostępne są serwisy oraz części zamienne.